Why? Because !
It often happens that we are going down a certain path, performing an action in a certain way, just because this is the way we have always done it, without knowing why.
Perhaps our parents have done so, perhaps our teachers taught us to do so, perhaps we watched too much TV and the shows have instructed us to do so… Perhaps that’s simply what we did the first time and it worked, and we didn’t ask too many questions… As they say, if it’s not broke – don’t fix it!
However, we wouldn’t have gotten anywhere with that attitude. Just think about it: with that attitude we would still be sitting in caves armed with stone axes. They worked very well, for millions of years.
This reminds me of a story I heard a long time ago, and no longer remember who told it to me. I beg whoever it was to forgive me, and to please remind me, if he/she is reading these lines and recognize it. I shall be happy to remember – and fix the reference. 🙂
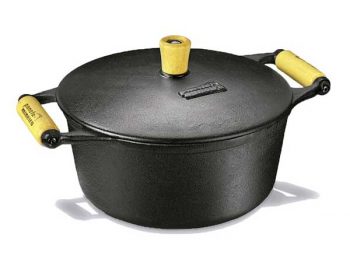

The corned beef story
A young couple got married, as it is wont to happen occasionally in various parts of the world. A short time after they got back from their honeymoon, they settled into their daily routine life together, and one of the regular things in daily life is meal preparation.
One day the young bride wanted to prepare her mother’s special corned beef dish which she could make just as well and which, she knew, her young husband favored. Young couples love doing everything together, and so the two of them went to the market and bought the meat and other ingredients,.
They brought the groceries home and began preparing together the favorite recipe, she – preparing the meat, he – cutting the vegetables. She took out the heavy pot from the kitchen cupboard, placed the meat on the cutting board, removed all the unwanted fat, and lined the pot with some of the vegetables he cut up. And then, just before placing the meat into the pot, she has done something which made her young husband very curious: she has cut off some of the long piece of meat at both ends, placing the two pieces in the pot, beside the large chunk of beef.
– Why did you cut the ends of the meat off? – asked the young man.
His wife shrugged. – Because, that’s how my mother always made this dish, – she said, filling the rest of the pot around the meat with the remainder of the vegetables and adding what needed to be added.
The young man was even more curious, and decided to ask her mother, at the next Shabbat dinner.
And truly enough, the next Friday night, when everyone has finished eating and were happy and satisfied, the young husband remembered the corned beef and asked his mother-in-law:
–You know how you cut the meat at both ends when you prepare your delicious corned beef?
– Indeed, I do, – she replied.
– Why do you do that? – asked the son-in-law.
– To tell you the truth, I haven’t really thought about it, but my mother has always prepared it that way, and so she taught me.
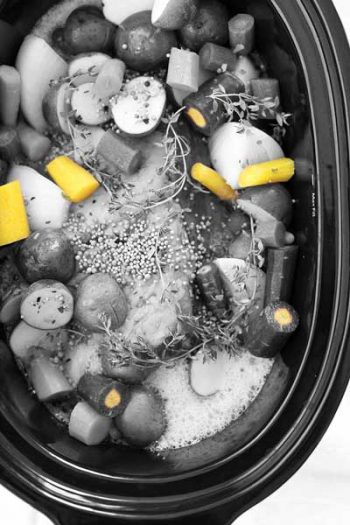
Now the young man was perfectly curious, and decided not to let the matter rest and to ask the grandmother. So the next holiday when they went to visit his wife’s grandparents, he has remembered and went up to the grandmother before the evening ended.
–Your granddaughter has made us your famous family corned beef recipe the other day, – he said. – There was something curious about the preparation, and I asked her about it, and she said it was what her mother always did. I asked your daughter, and she said it was as you always did. So I want to ask you: why do you always cut both ends of the meat before placing it into the pot?
–Ah, – the grandmother smiled and her eyes turned nostalgic. – My dear boy, when I was young and just got married, I did not have a trousseau, we did not have a lot of things. The only pot we had was too small for the whole piece of meat for my mother’s famous corned beef recipe. And so I would take the meat and cut off at both ends, to make it fit the pot. And I grew accustomed to doing that, and many years afterwards, when I had pots of the right size, I never changed the habit.
The million-dollar question
We often come to a new workplace where we find processes, defined “generations” of workers ago, and no-one remembers why and even when that was. The process simply goes on as it is, without us knowing why.
Most of us never even think to ask the question: why do we do it just so? We simply continue working in the set ways, habitually, out of inertia, and believe this is the correct and best way to work: after all, it has been working for X years, they must have had a reason…
And that really is the million-dollar question, which you need always ask, when you think about processes or wish to make changes.
As the daughter and granddaughter in our corned beef story discovered, there was absolutely no need to cut off the meat, and the habit was inherited from a different time, due to circumstances in the grandmother’s youth totally irrelevant to both her daughter and her granddaughter, who continued to carry on this “tradition” out of habit, unquestioningly, until the young man with a fresh look on the process has asked the question. Had he not asked, I’m sure their daughter would still have been cutting off the meat before placing it in the pot, as well. Not that there was something terribly wrong about the whole thing. I mean – cutting it, or not cutting it, who really cares, right?
But the very fact that we are doing some operation which is entirely redundant should be enough to make us stop and ask the question: Why? Why are we doing it just so?
Unnecessary actions are a waste
Eliminating the redundant operations from the process is one of the first steps in every lean manufacturing program. The 6 Sigma methodology, created by Motorola as a program for narrowing down the total process variance in an organization (and not only the technological ones, but any process at all), classifies process operations according to their contribution to the product or the process objective:
- An operation which adds value (Value-Added)
- An operation which doesn’t add value (Non Value-Added)
- An operation which doesn’t add value, but has business merit for the organization (Business Value-Added or Value-Added Required)
As part of the methodology, we examine and map the process and classify all its operation into one of the above types, and then move on to eliminate all those which do not add value to the process result.
Here I would ask to draw your attention to a vitally important point:
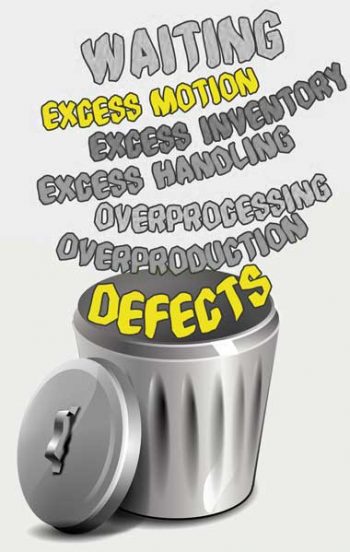

How do we classify the operations?
How do we know whether an operation truly adds no value to the process? Sometimes the answer is not as trivial as it appears, nor ever apparent. Thus, it is a stage which, while it seems simple, requires to be carefully considered.
And the first and most basic question we must ask is the one I asked earlier:
Why do we do it just so?
The answer mustn’t be “Because someone told us to”. The answer must give a clear reason to continue – or discontinue – doing it.
It could be tricky to discontinue an operation just because we do not understand why it was ever done. It is highly possible that whoever instructed to perform it knew what he was doing, and it is necessary for the process, even though we do not perceive the benefit. Remember the game from the previous article “Connecting the dots“? If the dots which include the significance of the operation to the process are not present in the picture we see, we would not understand why it is required!
Bandwidth
The range of vision for each of us in the entire picture is very limited. I call it “bandwidth”’ as in the concept we are familiar with from electricity or the Internet: defined as the quantity of information which can pass through at the same time. The definition for bandwidth in our case is very slightly different: it is the width of our view of the picture, the light beam that illuminates it. The wider it gets – the larger part of the picture and the clearer we see.
In the article “Connecting the dots” I have demonstrated our role in building the picture for all the team members, to show the process in its entirety. Here we can see an application of this principle of the wide and whole picture, demanding to know the reasons for the process being set as it is.
This is true for any aspect of our lives. We do not see the whole picture, but attempt to “fix” things, which are unclear to us by searching in the narrow and small lighted area visible to us.
A solution born of an immediate need
A few days ago someone has published on a Facebook page of our village community a call to the local municipal authority to stop planting “empty” trees in the public areas of our village, and replace them by fruit-bearing trees. “Imagine how nice it could be and how pleasant if we could pick lemons straight off the tree in the street? How much fun it could be for the children and all the opportunities for the neighbors to meet by the fruit trees”, she wrote.
She was motivated in this by the idea that whatever is not functional from the egocentric human point of view – her view – is empty, or unnecessary. Like a tree, which doesn’t bear fruit for us to eat is “empty”. I do not think that everything in life must be functional and useful, and not just useful – but useful for us, the use which we can understand! – or else it has no right for existence…
That said, without even touching on the subject of the process of planting and growing trees in a village, the difference in the maintenance and care required for fruit-bearing trees; or rather the variety of different maintenance and care requirements for different types of trees, which may not be suitable for uniform municipal system… Not touching on that subject because it would be the next stage in the discussion, after we already agreed that this a change is required, and now the particular obstacles in our way were to be addressed and overcome.
Human beings make a great deal of decisions in just such a manner. Importing animals from one habitat into another, to solve “a problem” we have with what lives there (cats to deal with mice; oysters to clear dirty water; etc). And afterwards, when the imported animals begin to multiply out of control and totally dominate the new habitat – we can no longer return things to how they were before, and start thinking again how to get rid of this new plague… A sort of Pandora box (or my mom’s freezer): once you opened it, what came out cannot be put back in it again.
But I digress. Let’s go back to the process, and the operations which add no value to it.
Unnecessary actions increase variance
Not only do redundant operations not add value to the process, they take value from it, or produce “negative value”. The reason for this is simply because each operation in the process creates variance. The additional variance may be very small and by itself insignificant, but it exists, and adds up. The more we interfere with the process, the more operations and operators there are – the more risks we introduce to the product (the result of the process). Therefore, by eliminating the redundant operations we clean the process up and render it more precise. The more precise the process – the lower its variance.
This is exactly the reason that 6 Sigma methodology employs this method: after all, its objective is lowering the total process variance. It is even implied in its very name (6 Sigma).
We shall talk of the 6 Sigma at length another time, this I promise. But right now I would like to focus on this one single stage: classifying the operations into those which add value, those which do not add value and those which do not add value but have business merit for the organization.
An operation which positively adds no value to the process result is a waste of resources. It takes time and work (same as money). It adds variance to the process (risk for non-conformance or damage, which cost additional money). It can also simply be… annoying! The worker is aware that the operation is not necessary, but he is required to perform it. He does not like to perform useless, meaningless work. Nobody likes to perform useless operations!
So what’s the bottom line here?
In the article “Investigate like children“, I have spoken to you about the importance of asking “Why?”.
And today, once again I say to you: ask “Why?”, and if the answer is “Because!” – start digging. It’s a gift for you: a sort of an X sign on the process map. The probability is high there’s treasure here for you to find!
And who would have thought one would dig for treasure in Quality Assurance? So have fun, ladies and gentlemen, have fun!
The corned meat picture: original picture taken from an article on instant pot corned beef at the FoodieCrush website.
Picture below it: stamp and envelope specially designed in Britain in 2002 to commemorate Rudyard Kipling, a British writer, specifically his book Just So Stories, here the story How the Leopard Got His Spots. The stamp’s postmark is also specially designed. From the British First Day Covers website.
The trees in Kfar Vradim picture was taken from an article by Shachar Danieli at the Homee webite.
This post is available also in:
עברית
You may also find interesting:
Powered by Contextual Related Posts