Connecting the dots
Today we shall learn to connect the dots. What dots? The dots which comprise the full picture. Which picture? The picture of our process. Any process you are dealing with right now, it makes no difference.
In this post I would like, with your permission, to go back and explore again the question of the very primary essence of the Quality Assurance profession, and what makes it stand out among other disciplines in the organization. What is so unusual about it? Why is it that nobody understands what we are actually supposed to be doing?
Well, in order to answer all these questions I must, first of all, go back and focus your attention on one of the greatest and ever-growing difficulties the world is facing in this new Age, the Age of Information.
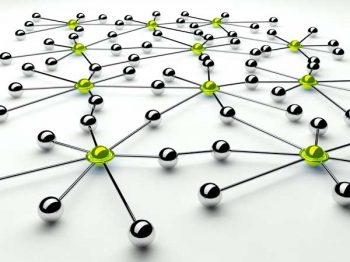
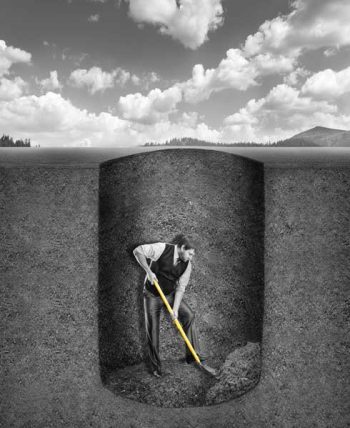
In-depth profession
The vast amount of information accumulated in every separate profession, which once had been a truly separate single one (engineer, doctor, lawyer, researcher etc.) has resulted in sub-division of each profession into sub-disciplines, and then these once again into sub-sub-disciplines… which evolved as narrow areas of expertise. The single general doctor has been replaced with dozens of medical professions; the lawyer – with dozens of legal specializations; the engineer – with dozens of narrow specific fields; researchers focus on a single small area of expertise…
I call such professions “in-depth professions”, for they dig into the depth in the same spot, and not widen their field. They concentrate enormous amounts of information on what is found deeper and deeper in this single spot, but do not see what is placed right by that spot, even on the surface. Do not take it into consideration, or include it in their picture of the area.
Now, I am not judging this situation at all, that would be pointless: it is neither good nor bad, it is just a fact of life at this time.
At the same time, this fact of life results in a reality where most professions specialize in a very narrow piece of their entire field, and the rest of the field becomes to them, beyond the very basics, a ”black box” or transparent.
The same thing and in an even more pronounced way occurs in organizations and plants, as well. Each department operates within its own specific narrow specialization, and whatever the others are doing is transparent to them. Taking, for example, all the officeholders among the wider middle management who are connected to a specific project or customer, we’ll see that the work of their colleagues, as well as all the other projects, is transparent or a “black box” to them. It’s like looking at the world through a telescope, fixed in place. You may see the spot it is aimed at perfectly and in the small detail, but outside it – there is nothing.
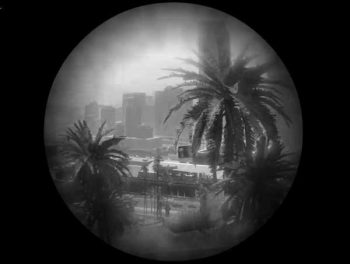
Width profession
The Quality Assurance profession, on the other hand, is different. It includes a lot of various types of fields and skills, which is the reason that education and academic degrees in their respective industries of work is not a mandatory requirement for QA engineers. Take me for example: I have worked in the electronics industry for years, with great success, and my background in electronics is not above high-school physics. If I see some components it is likely most would be unfamiliar to me, and I would surely have a hard time explaining how they operate.
I call professions of this kind “width professions”, for they cover wide areas and fields, but do not dig into great depths.
And why is that so essential?
Because the very essence of Quality Assurance is continuous improvement; improvement of processes, organizational processes. How does one improve a process if one does not see the whole process? Each of the people in the different departments connected to a specific project or customer can only see their own narrow and limited piece of the process, and not the whole process in its entirety. But how can one improve a process without understanding it? How can one see the whole picture when one is looking at it through a small and narrow hole?
Here enters the primary and most direct role of Quality Assurance: to create a wide and full picture of the whole process for each and every one of the people and connect them to that process in its entirety, in order to come up with the solutions to its improvement.
Connecting the dots
At this point I always take the example of a children’s game of “connecting the dots”, given to 5-year-old preschool children. Do you know it? The kids have a white page with numbered dots spread on it in seeming disarray. Only upon finishing connecting all the dots does the picture become apparent, and until then – it is difficult to guess.
This is not a random exercise merely to occupy the little one for half an hour and allow the adults a few moments of peace and quiet. It is an important developmental exercise in wide outlook and conclusion drawing ability.
Our process is comprised of many pieces of various information in all the organizational areas, technological processes and departments. Thus, not only is it this kind of a picture, made with dots, but they are not numbered, there are no instructions and their quantity may be great.
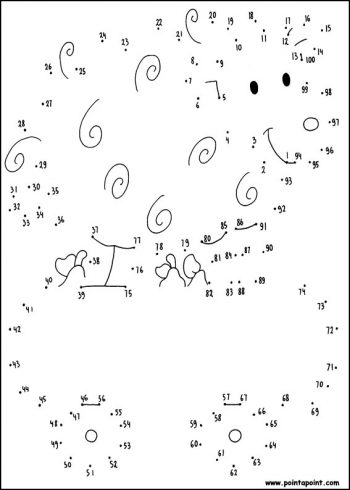
So what are we doing?
What we, in fact, are doing today in every possible area we choose to inspect is this: tearing the page with the dots into small pieces and handing them to various separate office holders or professions, and then – demanding they build the picture. Separately. Is there any chance of success? Well, statistically – perhaps there may be some tiny probability, totally random (and therefore non-reproducible) chance they may guess correctly. But we strive for a true process improvement, not a chance one, and one we can reproduce, right? Therefore the chances are more or less zero! We are, for all intents and purposes, setting them up to fail.
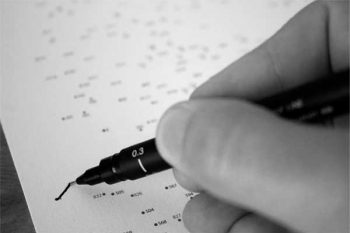
The QA engineer’s role is precisely this: bring all the people into one team with their respective pieces of the picture; put the pieces together like a puzzle, to make the whole picture. Then will the team be able to locate the true problematic places in order to find the solutions and ways to improve.
The QA engineer does not need the ability to dig deep into the technological process, for there is someone on his team whose specialty lies in that field. We need to combine the whole picture for everyone, then we may see the places of weakness, point the light there and direct the respective specialists to dig in those places.
To illustrate the matter I would like to make use of a work by the artist Thomas Pavitte, who draws portraits of celebrities or world-famous works of art by means of connecting dots. The picture at right is part of a drawing of Michael Jackson by Thomas Pavitte, named The Life of Michael Jackson, in its very early stages of connection.
Take a look at the picture and note that it is made of many dots in different colors. Let’s suppose that each color corresponds to the information available to each team member on his own. Now imagine the red dots missing from the picture, or there being only the green dots… Anyone thinking person will agree that the picture would not be made unless all its dots are present.
At the end of the article I have placed a little video, showing the artist Thomas Pavitte’s skillful hands connecting the dots to form the full drawing.
The same is true for our processes
The very same thing holds true for all organizational and other processes, with no exceptions; in health-related questions, country laws, and any processes you care to examine. Without the presence of all the dots, when each only has his own piece, we may expect, at best, patch-like solutions. These would be partial at best and mostly wrong, and while an attempt is made to correct one spot – another is in danger of being damaged. All due to the fact that the solution for the problem is being proposed by one who hasn’t examined the whole process, only his only little narrow spot with the light beam shining brightly on it, and therefore looked for a solution where the light is best, and not where the difficulty lies.
Only placing all the dots on the process map in its entirety will allow an efficient and long-term solution to the challenges in our processes.
And I would really like to be very precise in what I’m saying here:
Connecting the entire picture of the process is not a guarantee of success in solving the difficulties. However, failure to connect the entire picture is a guarantee of failure in solving the process difficulties, beyond a shadow of doubt.
So while your dot-connecting skill may be a bit rusty since you were 4-5-years-old, still the good news is that you have already done that once, and pretty easily, too. Also, you have since added a skill or too to your professional toolbox, which may come handy in reintroducing this fun process.
So go ahead, choose a process and begin connecting the dots! And don’t forget to have fun while you’re at it!
Panoramic photo of New York in 360 degrees taken from the top of the Empire State Building is taken from Wikipedia.
The pictures and video at the bottom of the article: the artist Thomas Pavitte in his work The Life of Michael Jackson, from the artist’s page on Behance website.
This post is available also in:
עברית
You may also find interesting:
Powered by Contextual Related Posts